Though trade liberalization creates many opportunities for developing countries and their marginalized people—like low-skilled Bangladeshi women garment workers who got the option to work in the garment (RMG) industry to earn money for their family—it also creates vulnerabilities for them which are largely responsible for health susceptibilities, mental pressure, low life standards, etc.
In the Bangladesh case, women RMG workers are very much prone to various risks because of working in unsafe garment factories and under unrealistic factory rules which increase their security dangers. It has therefore been explored in this study how far the rapidly growing garment industry is promoting violation of women garment workers’ rights.
Introduction:
Trade liberalization aims to make trade interactions easier between countries by removing existing trade barriers. This concept helped to make many rapid successes in the developing economies. Though it helps in improving developing countries’ economies, it’s not free from flaws. Liberalized trade policies are attracting more foreign investments to the developing countries generating more employment. The best part of this is that low-skilled women are getting more employment opportunities since labor-intensive export goods like in the readymade garments sector recruits low-skilled women workers. In this sense, trade liberalization provides opportunities for increasing women’s empowerment in the developing countries.
But it is not always the case in reality. While trade liberalization may offer opportunities to enhance women’s empowerment, at the same time, it can also create impediments that hamper women’s rights. In a labor-abundant developing country like Bangladesh, low-skilled women workforce is available at a very cheap price which in turn attracts foreign and local investors. For instance, though Bangladesh benefited a lot from trade liberalization by boosting its RMG sector, it also increased women’s vulnerabilities and promoted other factors like devaluation of work, etc.
Due to lack of complementary safety measures for avoiding health risks and factory safety measures for eliminating unexpected accidents that took many garments workers’ life in the past, trade liberalization, from this perspective, is unfortunately promoting degradation of women’s rights that assumes the nature of a threat for ensuring women’s development. This paper aims to analyze the conditions of women garment workers’ vulnerabilities due to liberalized trade policies and expansion of the garment industry in Bangladesh.
After the independence of Bangladesh, the government has been trying to implement privatization policies and other liberalized trade policies to cope with the world economy. Since Bangladesh is a labor-abundant country, government policies focused on the low-skilled labor intensive export goods sector. As a result, the garment industry gained the highest focus and became the largest export sector in Bangladesh. From the very beginning the RMG sector largely depended on low-skilled women workers because low skilled rural women are available at very low wages. Thus women became the main workforce in the garment sector.
Against that backdrop it’s worthwhile to examine how vulnerable is the situation of female garment workers’ in Bangladesh and how much the government’s liberalized trade policies regarding the expansion of the RMG industry and the MFA phase, post-MFA phase and GSP facilities have impinged on promoting women garment workers’ rights.
Background and Justification of the Study
Trade liberalization has a great deal of positive impact on developing countries’ economies and a success story for women’s development. But it is also noticed that at a certain point, trade liberalization creates obstacles for women’s development. By practicing free trade policies, marginalized and low-skilled women from developing countries can now have access to employment which is a big opportunity for them to develop. It is assumed that globalization and trade liberalization are universally beneficial and gender, class and race neutral. It is believed that trade policy measures are gender blind in orientation and gender neutral in effect. But it is also seen that trade liberalization has different effects on women and men because of their different access to and control of economic and social resources, decision making and participation.
These different results may occur simultaneously for different groups of women, or may occur at different phases of the trade liberalization process in the same country. To mesh in with a globalized world and get the highest benefits from liberalized trade policies and comparative advantage theory, developing countries are using their cheap labor which is mainly low-skilled women workers. This low skill and availability keep these female workers systematically underpaid which ultimately lower their life standard and increase their health vulnerabilities. Developing countries are therefore engaging more and more in the manufacturing sector promoting more women to work.
But the condition in the garment factories is not always as desirable as they should be. This unfavorable working condition leads to women’s health risks and to some extent life threatening accidents. The now-infamous Rana Plaza accident in Savar on April 24, 2013, became the deadliest accident in the history of the world’s industrial sector. This tragic accident has pointed to the fact that workplace safety and security for workers, even in the globally competitive RMG sector of Bangladesh, is far behind the required standard.
Since it is assumed that trade rules are gender neutral in their outcomes and impacts, according to BRIDGE report of 2005, national priorities for trade policies and negotiations have been determined without any gender analysis. This situation undervalues women’s work and encourages factory owners to retain unsafe factory conditions. Thus, factory owners do not value the rights of women workers since there are no strong policies to uphold women’s rights by ensuring essential factory safety measures, standard payment structure, standard working hours, etc within the trade liberalization policies. This situation ultimately promotes the violation of women workers’ rights instead of ensuring their rights and development.
Some conceptual gaps persist in the liberalized trade policies which are creating women’s workplaces more and more risky for them. This situation is now blamed for downgrading women’s development. Hence, it becomes necessary to explore the situation of Bangladesh garment workers’ condition in response to the rapid expansion of the RMG industry due to trade liberalization.
Bangladesh Government Initiatives to Support RMG Sector
Garment factories are, in fact, not new to Bangladesh since some factories existed from the Pakistan era. Hence after getting independence, Bangladesh owned some garment factories but these were not very well-functioning. In the newly independent country, the RMG factories had lack of trained workers and supervisors, and lack of capital and government support as well. This industry started functioning as a sound industry from the 1980s. At the beginning of the journey Korean manufacturers gave valuable training to the workers and invested in Bangladesh garment units. The most efficient and ground-breaking initiative was taken by President Hussein Muhammad Ershad in 1982. He first introduced the New Industrial Policy (NIP) which was the most important step toward the process of privatization.
Before 1982, the Bangladesh government followed the socialist idea and nationalized all industries; a plan which was a big obstacle for foreign investors to invest in the country. Then, President Ershad took a revolutionary step by implementing the concept of privatization. Many textile factories were privatized during the Ershad era. He also created the export processing zones (EPZs) for the first time in Bangladesh. The policy of privatization, denationalization of many textile industries and creation of export processing zones were the appropriate government initiatives taken by the then government which opened the path for the garment sector to develop to the highest level.
Another two important policies, i.e. the bonded warehouses and back to back letter of credit (L/C) facilities also played very crucial roles in the development of the Bangladesh RMG industry. The bonded warehouse facility had an important effect in eliminating duty-payment requirement and bureaucratic hassles and delays, while the new L/C facility also was a key support mechanism. It hugely facilitated opening L/C accounts in local banks for the import of inputs against the export orders placed in their favor by the final clothing importers. A third important policy support in the 1980s was the cash incentives through which clothing manufacturers received direct financial support.
Multi Fiber Agreement and Bangladesh Garment Sector
The development of the Bangladesh RMG industry largely depended on the 10-year period under the Multi-fiber Agreement (MFA). It was a short term measure that was introduced to adjust developed countries’ import from developing countries. Since developing countries have an absolute advantage in textile production because it is labor intensive and they have low labor costs, multi-fiber agreement gave them a greater opportunity to export their labor-intensive goods, mainly textile products, to the developed countries. Under this agreement, Bangladesh enjoyed no quota restriction for clothing and textile exports to the European Union, Norway, and Canada and none for textile exports to the United States.
In 1985, Bangladesh had to face quota restrictions for 30 product categories in clothing exports to the United States. It was imposed after a triple digit growth rate during the previous five years, with exports to the United States rising to $150 million. As a result, the absence of quotas for the EU market and relatively less restrictive quotas for the US market under the multi-fiber agreement guaranteed Bangladesh’s clothing exports.
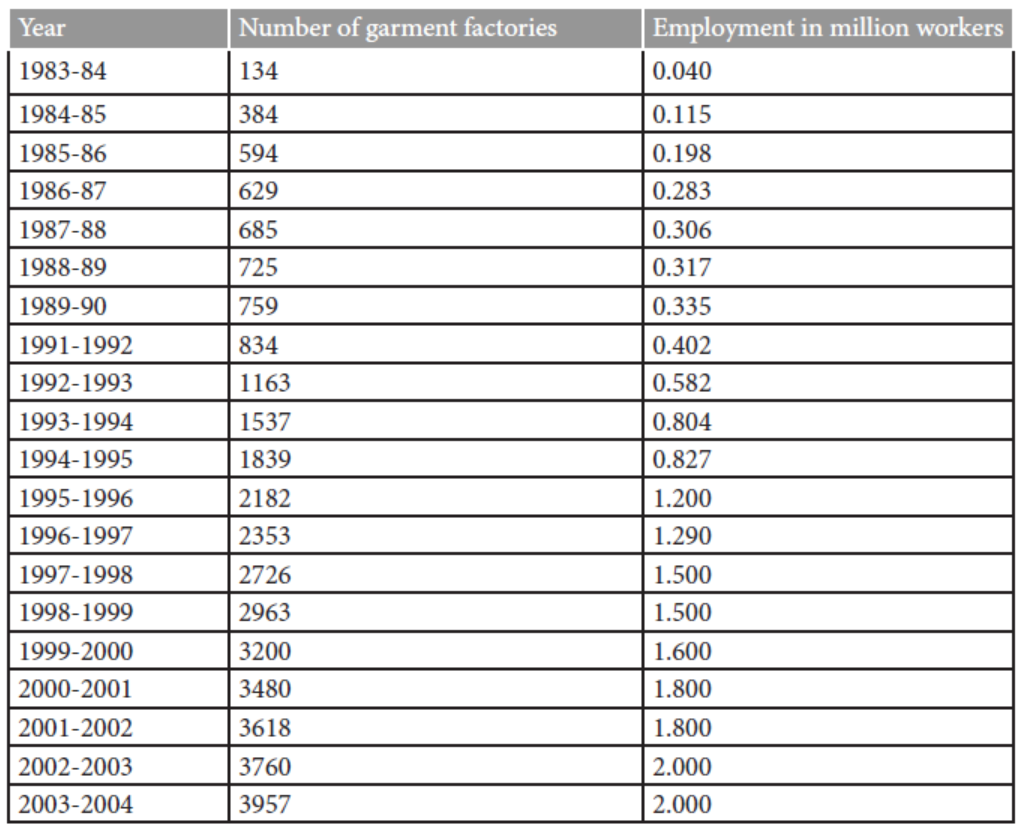
Source: BGMEA
Generalized System of Preference and Bangladesh RMG Industry
The preferential market access under the generalized system of preferences (GSP) played a significant role in the development of the Bangladesh garment sector. Bangladesh readymade garment products enjoyed preferential access to the EU market which was a big boost for this industry. For this preferential market access opportunity, the EU became the largest export destination of Bangladeshi readymade garment products. The percentage of export from Bangladesh reached higher peaks by the 1990s and by 2000, 50 percent of overall clothing export went to the EU. Since preferential market access requires the fulfillment of double transformation Rules of Origin (ROO) and many clothing exports, specifically woven products, could not fulfill this rule, the EU became the major importer of knitwear from Bangladesh.
Relevant figures demonstrate that the preferential market access under the Generalized System of Preference has played an enormous role in establishing a strong market in the EU which has been very helpful for the Bangladesh economy.
Post-MFA and Bangladesh Garment Sector
MFA played a very critical role in developing the LDC economies like that of Bangladesh by giving preferential access of developing countries’ labor intensive export products to the developed countries’ market. But the MFA was phased out on January 1, 2005, which was viewed as a big opportunity loss for the LDCs. However, Bangladesh managed to face the MFA phase-out problem and successfully maintained a notable growth after 2004. Though competition among the clothing exporters intensified significantly after the MFA phase out, Bangladesh managed to ensure the stable situation of its clothing export in the world market. Bangladesh is among the six countries (except China) which managed to ensure notable market shares in the US and EU markets after the MFA was phased out. The other countries are Cambodia, India, Indonesia, the Philippines and Vietnam.
Bangladesh had also successfully managed to face any big fall during the global economic crisis in 2008. Several effects, such as ‘Wal-Mart effect’ and the ‘China effect’ were taken into account to analyze Bangladesh’s success. Apart from this, Bangladesh’s main competitive advantage is the easy availability of low-skilled, low-cost labor. Consequently, labor cost had a big impact on the staying power of the RMG industry in Bangladesh compared to other labor intensive countries.
The minimum wage was increased to Tk 3,000 ($43) in November 2010, an increase of 80 percent, as a reaction to widespread labor unrest. Then, after the Rana Plaza tragedy on 24 April, 2013, the minimum wage was proposed to be increased to Tk 5,300 ($68) per month. But the owners are still not agreeing to the proposed wage increase. Due to severe protest, the minimum wage may go up to Tk 8,000 though owners are still offering Tk 3,600. It is anticipated that the wage board would set the pay between Tk 4,500 and 5,500.
The current minimum wage is too low compared to other countries. For that reason, buyers always rank Bangladesh as their lowest-cost source of supply. Mainly due to low-cost labor, Bangladesh managed to secure its favorable position in clothing exports after the MFA phase out and during the global economic crisis as well.
Expanding RMG Sector and Female Workers’ Rights
Though the expansion of the garment sector brings a wider opportunity for women to earn and to be employed, it also creates vulnerabilities for women workers which have long-term effects on the women workers’ life. In this part I have tried to explore the situation of Bangladesh female garment workers’ condition through reviewing the wage structure, health vulnerabilities and factory safety conditions that are mostly responsible for hampering women workers’ health and mental stability.
→Women’s Participation in the Garment Sector
The Bangladesh RMG industry recruits a large number of low-cost workers of whom 80% are women. Women workers who work in the garment factories are mostly young women with very little or no formal education or vocational training for the garment industry. These young female workers work as helpers who after a period of three to six months pick up skills and become machine operators. This is the common procedure by which young girls are incorporated in garment factory work. Since women workers are available at very cheap wages, the factory owners prefer women labor, especially young women workers since they are in abundant supply at a very low cost. Of the approximately 4.2 million workers in the RMG industry around 85% are women workers.
→Low wage causes low life standard
Young women are the most preferred choice of garment factory owners because they are not only available at very low wages but they can work hard. Though they work more, most of the time they are labeled as “helpers”. The work of these young women garment workers is the lowest paid job in the industry. Since their education level is very low too and most of them are not trained beforehand, they do manual work which is very hard labor and time consuming. Though they work hard, their wage never goes up.
The decision to increase the minimum wage was taken in response to a wave of strikes due to poor working conditions, low-life standards and sufferings which are caused by frequent factory accidents. The proposed minimum wage increased a lot compared to the last increase in 2010.
It is seen “the worker” below Grade 7 in the RMG industry minimum wage 2013 and “apprentice” in the garment factory minimum wage 2013 in the EPZs are the lowest paid workers. The worker below Grade 7 is a worker on probation (period of learning), and is not yet a formal member of the main work force. It is notable that young women work more as “trainees” and then as “helpers” and they have to work more than the older workers, but they are paid very less.
Previous research findings show that the number of women workers as “beginners” or “helpers” are more than trained workers. Factory owners prefer young women workers who work more as “helpers” because they claim that older workers perform poorly and make more mistakes. Since the number of “beginners” and “helpers” is higher, it is understandable that the majority of the workers, mainly women workers, are still paid very less. The position of Bangladesh compared to the rest of the world on minimum wage within the garment industry which demonstrate that the Bangladeshi workers are still the lowest paid workers in the world.

Monthly Minimum Wages (in USD) in garment industry of top apparel-exporting countries.(Bangladesh, Cambodia as of 2013)
Source: International Labor Organization
Conversely, research showed that, although men represent just 15% of the labor force in garment manufacturing, they have better paid jobs, such as general managers, production managers, line managers and supervisors. This demonstrates the gendered division of labor within the industry where women are able to access more lower paid jobs though women perform the hardest part of the manufacturing process.
Thus it is seen that due to low wage, female garment workers have to face severe hardships in their daily life.
→Discrimination in overtime payment
Women workers have to work overtime which is compulsory for them to meet the target production. According to Bangladeshi law, workers are supposed to work an eight-hour shift. However, garment workers are forced to work extra hours on a daily basis in order to meet production targets set by factory owners. Findings showed that around 80% of women workers leave their factory between 8pm and 10pm after starting work at 8am, violating Bangladeshi labor laws which state that under no circumstances should daily working hours exceed 10 hours.
The worst part is after doing overtime, women workers often remain unpaid. It is because factory owners cut their overtime payment whenever they want. Reasons given for these illogical cuts include lack of punctuality, failure to meet production targets, unnecessary conversation with co-workers, absence without leave, making mistakes at work or protesting management decisions. Female workers are cheated more often than men, as they are seen as quieter and less likely to complain.
It is also noticed that only a small number of the workers receive letters of appointment, while most of them carry a factory identity card. These are legal requirements that serve as evidence of employment and form the legal framework enabling workers to claim their basic labor rights such as the right to receive a wage and payment for overtime. But sometimes workers who do not have letters of appointment, become victims of cheating while getting overtime payment.
→Women workers’ health risk
Women workers in the RMG industry have to face severe health related complications due to unsafe factory conditions, factory owners’ stringent rules, frequent overtime work along with daily long working hours, absence of maternity leave, etc.
Most of the factory owners do not follow the 2006 Bangladesh Labour Law, which protects the right to maternity leave. In 2011, the Prime Minister of Bangladesh announced that maternity leave would be extended to six months, but it remains unclear whether this will be implemented outside the civil service. For that reason, factory owners set various types of maternity leave provisions which are not favorable to the women workers.
Thus this necessary right to maternity leave has long been breached. Furthermore, many factory owners pay less to the women workers during this special period which is much less than the legal right. A worse consequence is that most of the time women workers have to lose their job after giving birth. In some factories, the owner accepts women workers returning to work after giving birth but they have to work at a lower grade. They cannot work at their previous grade.
Another inhumane practice which impacts most of the women workers is that many of them are forced to work during the final stages of pregnancy to meet the production targets which seriously hampers the health of both mother and child.
Long working days along with frequent overtime work create a heavy load for women’s health. It destroys necessary rest periods. It creates hurdles for needed domestic work. Most of the time women workers have to go to their home late at night and again come back to the factory for work early the next morning. It puts a great load on them as they have to complete their household chores within a very short time. It also takes away time to spend with their children and other family members.
Naturally, these excessive pressures have an adverse impact on women workers’ health and mental stability. Women workers reported concerns over long periods of separation from their children, particularly for women with young children who are breastfeeding. The combination of long work days and frequent night shifts severely affects the health, family life and reproductive health rights of women garment factory workers.
It should also be noted that a factory with more than 300 workers must by law have medical and nursing staff on site during all working hours. But the reality is that in Bangladesh garment factories, there is no system to keep a doctor or nursing staff or any kind of medical assistance. Thus in case of an accident or any kind of emergency factories do not have any medical treatment facility available for the support of workers.
→Garment factory condition increases women workers’ risk
Though the Bangladesh garment industry developed a lot in terms of quality production and securing stable market access to the developed countries, garment factories’ safety condition is not complementary. The Bangladesh garment factory safety record has been marked as the worst due to frequent factory accidents. The Bangladesh Fire Department recorded that 414 garment workers were killed in 213 factory fires between 2006 and 2009. Not only fire related accidents occurred in the garment factories, there are also accidents due to poor building standard, poor emergency procedures, inadequate and blocked fire exits and overcrowded work places.
Since the Bangladesh garment industry has become the backbone of the country’s economy by producing around 80% of the country’s export, large number of factories has been engaging in garment production rapidly; around five thousand garment factories are operating currently ranging from large first tier suppliers to small factories.
Since this industry is characterized by low cost, fast production and cheap labor, more and more local investors are interested to be involved in this sector. Women workers who work in the garment factories at a low pay are very much poor. Due to lack of alternative employment options, these poor women have to work in garment factories even if they are poorly paid and have to work in unsafe factory conditions that fail to fulfill the basic standards of health and safety.
As the majority of the garment workers are women and they are easily available, factory owners do not pay attention to factory safety measures to ensure these women workers’ rights. To maintain a high percentage of profit, some factory owners often build their factories without following basic standard requirements. Additionally the rapid expansion of the industry has promoted the illegal conversion of buildings into factories without the permission of the responsible authority or without fulfilling basic building safety requirements.
In many instances factory owners added extra floors to the factory to create extra space for the workers and machines. Generally, factory owners build or renovate their factories in a very short time and at a cheap cost that results in major safety problems such as faulty electrical circuits, unstable buildings, inadequate escape routes and unsafe equipment.
The notorious Rana Plaza tragedy is the deadliest example of poor building construction. Due to factory owner’s and building owner’s lack of awareness about the poor condition of the building, the eight-storied building collapsed killing thousands of workers with many thousands more left severely injured. This accident has been marked as the deadliest garment factory accident in world history as well as the deadliest structural failure in the modern human history.
The root causes of this deadly incident were mainly the poorly and cheaply built building with heavy machines and the presence of a huge number of workers. There were also visible cracks in the building but the factory owner and the building owner ignored these signs and ordered the workers to continue their work. Because of greed and lust for profit, no attention was paid to the safety of the workers which later resulted in so many deaths.
Concluding remarks
The Bangladesh readymade garment industry is the backbone of the country’s economy. It also provides good employment opportunities to the poor, low skilled women workers. While it does provide low-skilled women workers the ability to earn by themselves, it also creates several vulnerabilities related to health, life standard and life threatening risks. Findings showed in this article that factory owners’ desire to gain profit by making poorly constructed buildings, retaining unsafe factory environment, imposing strict rules for the workers to attain production targets, neglecting women workers’ health rights, etc. have made the entire work environment dangerous and insecure for women.
Since the concept of trade liberalization is gender neutral and there are no specific and strong policies to ensure women workers’ rights in the free trade policies, garment factory owners do not feel accountable for their deeds. There is also wage discrimination between male and female workers. The buyers’ responsibility in upholding women workers’ rights are also very much important. Thus, the poor women workers of Bangladesh will be greatly benefited if all the stumbling blocks are taken in consideration. Moreover, proper coordination between national and international measures should be ensured to uphold women RMG workers’ rights.
It is wonderful and very useful for our nation & for my research also..
Hi Shanjida,
You have written a nice long informative article for us. And I loved it. Because you really think about for garments workers. I appreciate your effort.
Thank you for the thorough history and context of your analysis. Do you have sources and citations for the information you reference? I would like to cite your work but I cannot do so unless your information is verified.